قالب گیری دورانی (به انگلیسی: Rotational Molding) یکی از فرآیندهای شکلدهی در صنعت پلاستیک است که کاربردهای بسیاری دارد. یکی از مراحل مهم در این روش قالبگیری، فرآیند سرد کردن مخزن پلی اتیلن یا تانکر آب پلاستیکی است که در کیفیت محصول نهایی بسیار تاثیرگذار است، از این رو ما تصمیم داریم به بررسی تاثیر نحوه سرد کردن مخازن پلی اتیلن در این مطلب بپردازیم.
قالب گیری دورانی (Rotational Molding)
از این روش قالبگیری در اواخر سال ۱۹۵۰ میلادی و با استفاده از پلیمر پلی وینیل کلراید (PVC) آغاز شد که رفته رفته این پلیمر جای خود را به پلی اتیلن (PolyEthylene) داد. از کاربردهای اصلی این روش، همانند قالبگیری دمشی (Blow Molding) و شکلدهی گرمایی (Thermoforming)، میتوان به تولید قطعات پلاستیکی بزرگ و توخالی اشاره کرد. انعطافپذیری در طراحی و مقیاس محصولات، کاربرد این روش قالبگیری را بسیار گسترده کرده است، به طوریکه از ظروف ذخیره و بستهبندی ساده گرفته تا محصولات پیشرفته خودرو، پزشکی و هوافضا از این روش برای تولید محصولات متنوع خود استفاده میکنند.
از دیگر روشهای قالبگیری یا شکل دهی مواد اولیه پلاستیکی میتوان به قالبگیری فشاری و تزریقی اشاره داشت.
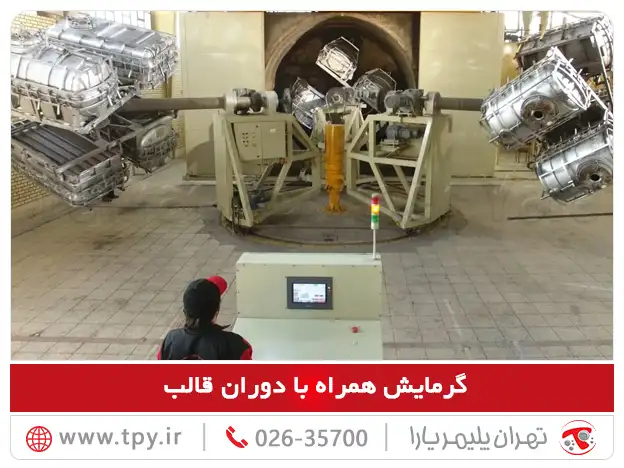
قالب گیری دورانی
مراحل قالبگیری دورانی (چرخشی)
این فرآیند دارای ۴ مرحله است که به شرح زیر میباشد:
- قرار دادن پودر پلیمر داخل قالب
- گرمایش همراه با دوران قالب و بازوی نگهدارنده قالب
- سرد کردن قالب تا رسیدن به حالت جامد و شکل مطلوب
- باز کردن قالب و خروج محصول از قالب
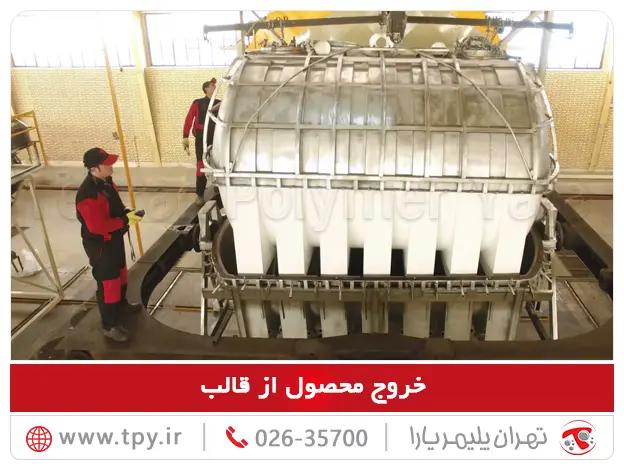
خروج محصول از قالب
۱. قرار دادن پودر پلیمر داخل قالب
از انواع مختلف پلیمر، پلی اتیلن بیشترین کاربرد را در ساخت قطعات با این روش دارد. این فرایند با سایر فرایندهای شکلدهی پلاستیک نظیر تزریق پلاستیک تفاوتهای زیادی دارد. از جمله تفاوتهای این روش با سایر فرایندها میتوان به تنش برشی صفر، گرمایش طولانی مدت، سیکل طولانی تولید، سرعت سرد کردن بسیار آهسته و حضور اکسیژن در تماس با سطح داخلی قالب در حین فرایند اشاره کرد. این شرایط تولید، ریز ساختار (ریختار) منحصر به فردی ایجاد میکند که به طور مستقیم روی رفتار مکانیکی محصولات تولید شده با این روش مؤثر هستند.
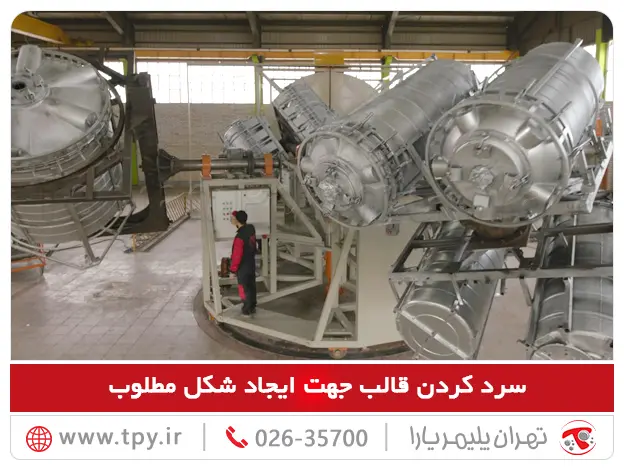
خروجی قالب پس از سرد کردن
۲. گرمایش همراه با دوران قالب و بازوی نگهدارنده قالب
همانطور که اشاره شد، یکی از ویژگیهای این روش، گرمایش طولانی مدت است که میزان این گرمایش میتواند تأثیر زیادی در رفتار مکانیکی قطعات تولید شده با این روش داشته باشد. در این فرایند گرمایش ناکافی به علت پخت ناکامل ذرات پودری پلیمر، باعث ایجاد حفره و حباب در ساختار پلاستیک میشود که سطح ناصاف و زبر و همچنین وجود حفرههای عمیق حبس شده داخل پلیمر را به همراه دارد.
گرمایش بیش از حد در این فرایند به تخریب سطوح داخلی منجر می شود که این تخریب با حضور قله گروههای کربونیل، وینیل و هیدروپراکسید در آزمون طیف سنجی (FTIR) قابل شناسایی است. این تخریب همچنین از تغییرات گرانروی پلاستیک تخریب شده مشهود است. در پلی اتیلن، تخریب باعث افزایش گرانروی میشود، زیرا شاخههای جانبی پلی اتیلن پس از تخریب، تشکیل اتصالات عرضی میدهند. تخریب در پلی اتیلن باعث میشود، ساختار بلوری به شدت تغییر کرده و ساختاری ناکارآمد ایجاد کند. در واقع این اصلاحات ریزساختاری با کاهش دمای ذوب انجام میگیرند که نشاندهنده افت کارایی ساختار بلوری است. بنابراین هم حبابهای ناشی از گرمایش ناکافی و هم تخریب ناشی از گرمایش بیش از حد در شکنندگی و کاهش استحکام قطعات تولید شده به روش قالبگیری دورانی تعیینکننده هستند.
ریختار نهایی در محصولات پلیمری نقش حیاتی در تعیین ویژگیهای مکانیکی این محصولات ایفا میکند. ارتباط میان اجزای اَریخت و اجزای بلوری در پلیمرهای نیمه بلوری، ویژگیهای فیزیکی پلیمر را کنترل میکند. ساختار پلیمر، به عنوان مثال: میزان شاخهای بودن، میتواند روی درجه بلورینگی نواحی بلوری تأثیرگذار باشد. علاوه بر ساختار پلیمر، شرایط فرایندی به میزان زیادی روی میزان بلورینگی تأثیرگذار است. در فرایند قالبگیری دورانی، شرایط فرایند بدون تنش و همچنین زمان فرایند طولانی این اجازه را به پلیمر میدهد که ساختارهای گویچهای کلاسیک ایجاد کند. زمانی که گویچه هسته گذاری میکند، آنقدر رشد میکند که به گویچه کناری برسد.
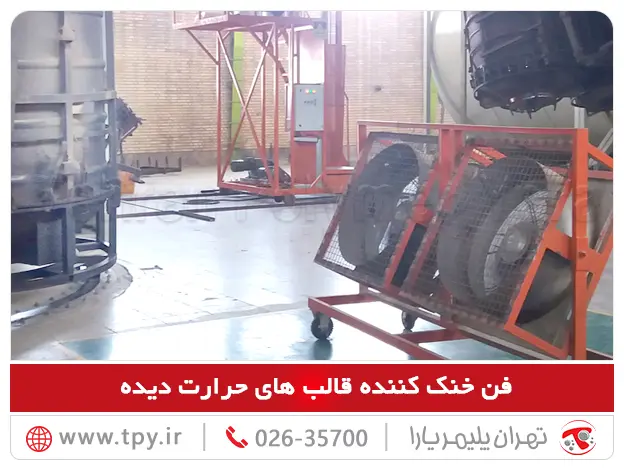
بررسی سرد کردن قالب مخازن
۳. سرد کردن قالب تا رسیدن به حالت جامد وشکل مطلوب
به طور کلی، بلورینگی قطعات قالبگیری شده به روش دورانی تحت تأثیر نرخ سرد کردن قرار دارند. آهسته سرد کردن منجر به محصولاتی با بلورینگی بالا و چگالی هسته گذارای پایین در دماهای بالاتر میشود که نتیجه آن گویچه های بزرگتر است. در محصولات تولید شده به روش قالبگیری دورانی؛ این نکته کاملاً مشخص است که سطح داخلی این محصولات، گویچههای بزرگتر و بلورینگی بالاتری دارند، زیرا آهستهتر از سطح خارجی سرد میشوند. علاوه بر این، گویچههای سطح داخلی قادر هستند، آزادانه رشد کنند و تماسی با دیواره قالب ندارند.
این عوامل سبب میشود سطح داخلی محصولات قالبگیری شده به روش دورانی دارای بافت خشن باشند. در سطح خارجی، رشد گویچهها به واسطه حضور دیواره قالب محصور شده است و برخی ساختارهای بلور تبادلی (Trans Crystalline) میتوانند توسعه پیدا کنند. در جایی که پلیمر روی دیواره قالب، بلورینه میشود، ساختار بلور پلیمر میتواند متأثر از تخریب در حین قالبگیری دورانی باشد. تخریب، تمایل دارد روی سطح داخل قالب رخ دهد و میتوان با مشاهده ریزساختارها در سطح داخلی، آن را شناسایی کرد. در پلیمر بکر، گویچهها اندازه مشابه و ساختار منظمی دارند. زمانی که پلیمر تخریب میشود، گویچهها کوچکتر میشوند و با افزایش تخریب، ساختار گویچهها شکسته شده و پلیمر به سمت اَریخت شدن پیش میرود .
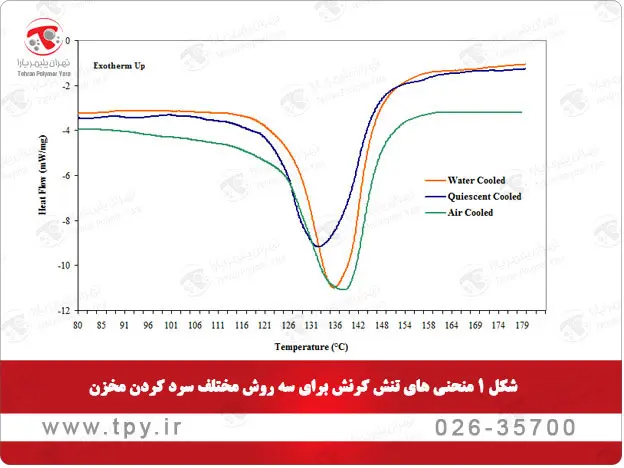
سرد کردن محصول پس از قالب گیری
در اثر سردکردن سریع، گویچه های کوچکتر با میزان بلورینگی پایین تر ایجاد می شود. گویچه ها و نواحی بلوری کوچکتر، افزایش مولکول های چسبنده درون بلور را نتیجه می دهد که باعث بهبود خواص چقرمگی مواد میشود. به طور کلی درک بهتر رفتار شکست به همراه آزمون استحکام، برای تأمین اطلاعات لازم از فرایند رشد ترک در مواد، امری ضروری است که می تواند به طور مستقیم روی کارایی محصول در شرایط کاربری واقعی اثر گذار باشد.
وزن مولکولی بالاتر، توزیع جرم مولکولی پهن تر، نواحی اَریخت و بلور ضخیم تر، از دیگر عواملی هستند که در بالاتر بودن میزان چقرمگی شکست در پلی اتیلن قالبگیری شده به روش دورانی مؤثر هستند. وزن مولکولی بالاتر و توزیع جرم مولکولی پهن تر به دلیل افزایش گره خوردگی ها، چقرمگی شکست را بهبود می دهند. ناحیه اَریخت ضخیم تر تشکیل ریزحفره ها (Micro voids) را آسان تر می کند که جذب انرژی بالاتر می رود و در نتیجه چقرمگی شکست افزایش می یابد. کارایی بیشتر بلور در بلورهای ضخیم تر و همچنین مشارکت در ایجاد ریزحفره های نواحی اَریخت، چقرمگی شکست را بالا می برد.
۴. باز کردن قالب و خروج محصول از قالب
در این مرحله بعد از سرد شدن قالب نخست قلاب های اطراف مخزن را باز نموده و بسته به نوع قالب ، سنگینی و سبکی ،به شیوه های گوناگون توسط نیروی انسانی و یا جرثقیل های سقفی اقدام به تخلیه این مخازن میکنند.
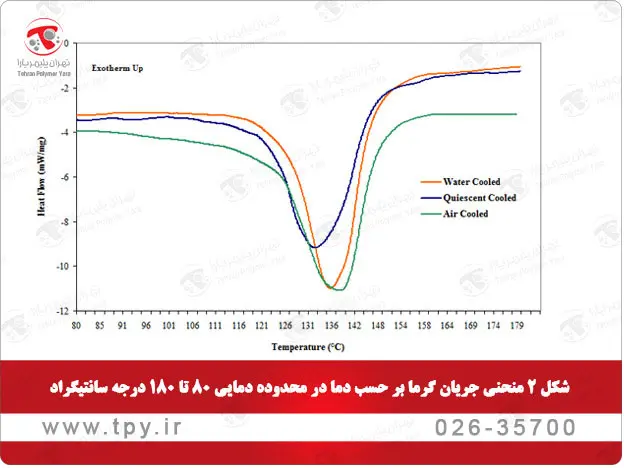
جریان گرما بر حسب دما در قالب گیری دورانی
ویژگی مخازن پلی اتیلن تولید و سرد شده به روش روتیشنال
به طورکلی مخازن نگهداری آب و مایعات تولید شده به روش قالبگیری دورانی میبایست از لحاظ ویژگیهای زیر دارای حد مطلوب باشند:
- میزان کشیدگی در نقطه پارگی بالا
- دمای نرمشدگی بالا
میزان کشیدگی در نقطه پارگی بالا
با توجه به اینکه این مخازن به طور متناوب و مکرر در حال پر و خالی شدن هستند، انعطاف پذیری بالا به حفظ طول عمر بالای این محصولات در برابر تنش های ناشی از این پر و خالی شدن کمک فراوانی خواهد کرد. همچنین مقاومت در برابر رشد ترک های محیطی نیز ارتباط مستقیم به میزان انعطاف پذیری محصول دارد و هرچه انعطاف پذیری بالاتر باشد این مقاومت بالاتر خواهد بود.
دمای نرمشدگی بالا
با توجه به کاربری مخازن در شرایط دمایی مختلف، هرچه دمای نرمشدگی مخازن بالاتر باشد کاربری آنها نیز بالاتر خواهد بود.مقاله حاضر سعی در مطالعه و بررسی چگونگی اثرگذاری نحوه سرد کردن به عنوان یکی از مهمترین پارامترهای فرایندی تحت کنترل در تولید مخزن پلی اتیلن بر رفتار مکانیکی و حرارتی و اطمینان از انتخاب روش فرایندی مناسب با بالاترین خواص مکانیکی و حرارتی دارد. بنابراین در این پژوهش اثر روش های مختلف سرد شدن مخزن پلی اتیلن بر ویژگی های حرارتی و مکانیکی بررسی شد و از چندین شیوه ی تخصصی مانند اندازه گیری نقطه نرم شدگی (Vicat) و آزمون حرارتی گرماسنجی پویشی تفاضلی(DSC) به منظور دستیابی به بهترین روش سرد کردن استفاده شد.
مواد اولیه استفاده شده در قالبگیری فشاری
پلی اتیلن (PolyEthylene) مورد استفاده در تولید مخازن از طریق قالبگیری دورانی، پلی اتیلن با جرم مولکولی متوسط (MDPE) گرید HD 3840 UA ساخت پتروشیمی تبریز است. چگالی این گرید از پلی اتیلن g/cm3 938/0 و نرخ جریان مذاب آن تحت دمای °C 190 و وزنه ۱۶/۲ کیلوگرم برابر g/10min 4 است.
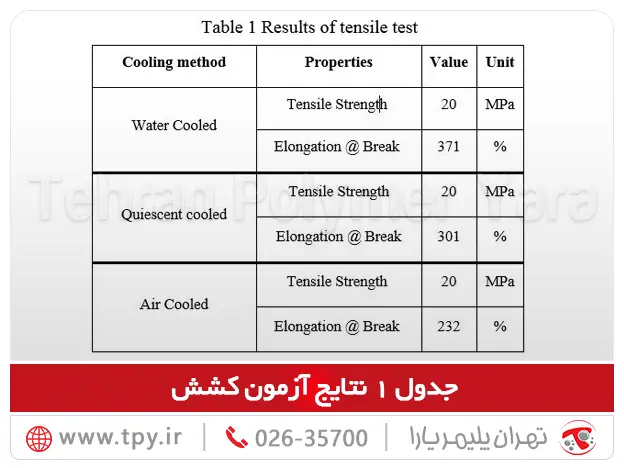
نتایج آزمون کشش
روش تهیه نمونهها
مخازن از طریق قالبگیری دورانی در کوره کاروسل (Carousel) با سرعت چرخش قالب ۸ دور بر دقیقه و سرعت چرخش بازو ۳ دور بر دقیقه با دمای °C 200 و در حجم ۵۰۰ لیتر به مدت ۳۵ دقیقه قالبگیری شدند. از پودر پلی اتیلن برای تولید مخزن به مقدار ۲۰ کیلوگرم استفاده شد. ضخامت نهایی محصول به دست آمده mm 5 است.
سه روش مختلف سردکردن در این مطالعه مورد بررسی قرار گرفت :
- سرد کردن باآب، قالب با استفاده از دو واترجت سرد شد. (Water cooled)
- سرد کردن با هوا، قالب با استفاده از یک دمنده هوا سرد شد. (Air cooled)
- سرد کردن ساکن، هیچ خنک کننده ای استفاده نشد. (Quiescent cooled)
دما حین سرد شدن قالب در نقطه دیواره قالب ثبت شد تا نرخ سرد شدن به دست آید. این اندازه گیری ها سرعت °C/min 38 برای سرد کردن با آب، °C/min 18 برای سرد کردن با هوا و °C/min 13 برای سرد کردن ساکن را به دست دادند. پس از تولید، نمونه های آزمون کشش با استفاده از دستگاه پرس هیدرولیک و تیغه دمبل کاتر نوع 1BA مطابق استاندارد ISIRI 6621-1 از روی مخازن پانچ شدند. جهت آزمون های Vicat، DSC و چگالی نیز نمونه گیری از روی مخازن تولیدی انجام گرفت. جهت آزمون MFI، نمونه گیری از سطح خارجی محصول انجام شد. جهت انجام آزمون ضربه چارپی، نمونه ها با استفاده از دستگاه پرس هیدرولیک به صورت نوع ۱ مطابق استاندارد ملی شماره ۱-۹۲۷۷ از روی مخزن پانچ شد و با استفاده از دستگاه ناچ زن، شکاف نوع A مطابق استاندارد ملی شماره ۱-۹۲۷۷ روی آن ایجاد شد.
روشهای آزمون
برای انجام آزمون کشش از دستگاه کشش یونیورسال ساخت شرکت اسپیکو کشور ایران استفاده شد. این آزمون در دمای اتاق با سرعت فک متحرک mm/min 50، فاصله اولیه بین دو فک mm 25 و تعداد ۵ تکرار از هر مخزن انجام شد. کشش نمونه تا زمان گسیختگی کامل آن ادامه پیدا می کرد. نتیجه نهایی حاصل از آزمون کشش برای هر مخزن از میانگین ۵ عدد ناشی از ۵ تکرار به دست آمد. این آزمون مطابق استاندارد ISIRI 6621-1 انجام شد.
آزمون حرارتی نمونه ها به وسیله دستگاه تحلیل حرارتی مدل 1052B ساخت شرکت SKZ کشور چین طی فرایند رفت از دمای محیط تا دمای C° ۲۰۰ با سرعت C/min° ۱۰ تحت جو نیتروژن انجام شد. نمونه ها به منظور اندازه گیری DSC در پن آلومینیومی قرار داده شد. این آزمون مطابق استاندارد ISIRI 7186-6 انجام شد.
دمای نرمشدگی وایکات با استفاده از دستگاه Vicat ساخت شرکت اسپیکو کشور ایران تحت بار ۵۰ نیوتن و با سرعت گرمادهی °C/h 120 به دست آمد. این آزمون مطابق استاندارد ISIRI 6982 انجام شد. از هر مخزن دو نمونه اندازه گیری شد. عدد گزارش شده میانگین دو اندازه گیری است.
نرخ جریان مذاب با استفاده از دستگاه MFR ساخت شرکت بن افزار کشور ایران تحت دمای ºC 190 و وزنه ۱۶/۲ کیلوگرم اندازه گیری شد. این آزمون مطابق استاندارد ISIRI 6980-1 انجام شد. مقدار ۸ گرم از هر نمونه مورد اندازه گیری قرار گرفت. اندازه گیری ها بعد از ۵ دقیقه پیش گرم و با فاصله زمانی هر ۲۰ ثانیه انجام شد. مقدار گزارش شده به عنوان نرخ جریان مذاب، میانگین ۱۰ اندازه گیری است.
چگالی نمونه ها با استفاده از دستگاه ترازوی چهار صفر مجهز به کیت چگالی سنج ساخت شرکت AND کشور ژاپن و با استفاده از آب دوبار تقطیر به عنوان مایع غوطه وری و در دمای ºC 23 اندازه گیری شد. این آزمون مطابق استاندارد ISIRI 7090-1 انجام شد. مقدار گزارش شده به عنوان چگالی نمونه ها، میانگین ۱۰ اندازه گیری است.
آزمون ضربه چارپی با استفاده از دستگاه آزمون ضربه چارپی ۱۷ ژول ساخت شرکت بن افزار کشور ایران مطابق روش 1eA استاندارد ملی شماره ۱-۹۲۷۷ در دمای ºC 23 انجام شد. از هر مخزن ۱۰ نمونه اندازه گیری شد. عدد گزارش شده میانگین ۱۰ اندازه گیری است.
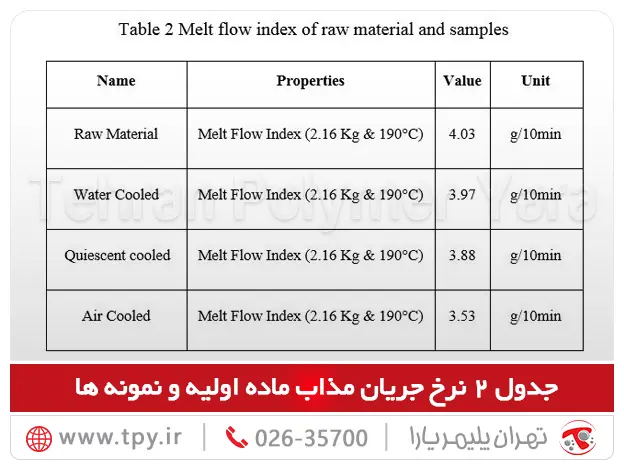
جدول بررسی سرما و گرمای قالب گیری
آزمون کشش
مطابق نتایج نشان داده شده در نمودار ۱ و داده های جدول ۱، در هر سه روش سرد کردن، محصولات دارای استحکام کششی یکسانی بودند. درحالیکه در میزان کشیدگی در نقطه شکست، اختلاف قابل ملاحظه ای متأثر از نحوه سرد کردن ایجاد می شود. میزان کشیدگی در نقطه پارگی، ارتباط مستقیم با ساختار بلور در پلی اتیلن دارد. سرعت سرد کردن آهسته تر، بلورینگی بالاتر را نتیجه می دهد که اثرات مضری روی رشد ترک دارد. در واقع بلورینگی بالاتر، گویچه های بزرگتر و کاهش انعطاف پذیری را نتیجه می دهد. با توجه به یکسان بودن ماهیت پلی اتیلن در سه نمونه بالا و همچنین شرایط یکسان تولید برای هر سه نمونه (تنها تفاوت در نحوه سرد کردن وجود دارد)، می توان نتیجه گرفت که ساختار بلور در نمونه سرد شده با هوا، ساختاری ناکارآمدتر نسبت به ساختارهای بلور در دو نمونه دیگر دارد.
ساختار بلور پلیمر می تواند متأثر از تخریب در حین فرایند قالبگیری دورانی باشد. تخریب تمایل دارد روی سطح داخل قالب رخ دهد و می توان با مشاهده ریزساختارها در سطح داخلی آن را شناسایی کرد . در واقع در نمونه سرد شده با هوا، ساختار بلور در اثر تخریب سطحی به ساختاری ناکارآمد تبدیل شده است.
با نگاهی به نحوه سرد کردن محصول متوجه علت این تخریب سطحی خواهیم شد. محصول پس از خروج از کوره دارای دمایی در حدود °C 200 است که در این دما پلی اتیلن مستعد تخریب است. زمانی که محصول در معرض هوای ساکن و در دمای محیط سرد می شود، مدت زمان بیشتری در مقایسه با روش سرد کردن به وسیله هوا، محصول در معرض اکسیژن قرار دارد ولی چون در روش سرد کردن با هوا، اکسیژن با سرعت بالا به محصول مستعد تخریب دمیده می شود، تخریب بیشتری را در نمونه سردشده با هوا شاهد هستیم.
در واقع این تخریب روی سطح خارجی مخزن ایجاد شده که منجر به ایجاد ریزساختار در این سطح و ناکارآمدی ساختار بلوری در این سطح می شود. این ناکارآمدی ساختار بلوری منجر به کاهش چقرمگی در کل محصول می شود. بنابراین پایین ترین میزان کشیدگی در نقطه پارگی مربوط به این روش خواهد بود.
آزمون نرخ جریان مذاب
به منظور بررسی تخریب سطحی در نمونه ها، از آزمون نرخ جریان مذاب استفاده شد. برای این کار از سطح خارجی محصولات نمونه گیری انجام شد. همانطور که از نتایج مشخص است در سطح خارجی نمونه سرد شده با هوا شاهد تخریب هستیم که این تخریب خود را با کاهش نرخ جریان مذاب نشان داده است. در واقع نتایج آزمون نرخ جریان مذاب تأییدی بر نتایج آزمون کشش است. به منظور مقایسه بهتر، نرخ جریان مذاب مواد اولیه (پلی اتیلن گرید ۳۸۴۰ پتروشیمی تبریز) نیز اندازه گیری شد.
در پلی اتیلن، تخریب باعث افزایش گرانروی می شود زیرا شاخه های جانبی پلی اتیلن پس از تخریب، تشکیل اتصالات عرضی می دهند. تخریب در پلی اتیلن باعث می شود ساختار بلوری به شدت تغییر کرده و ساختاری ناکارآمد ایجاد کند. در واقع این اصلاحات ریزساختاری با کاهش دمای ذوب انجام می گیرند که نشان دهنده افت کارایی ساختار بلوری است.
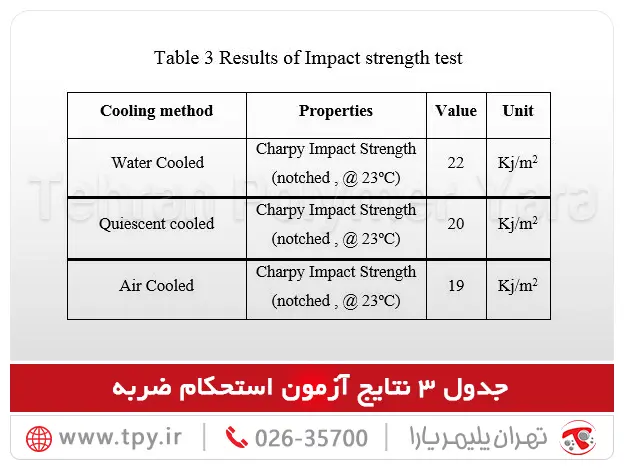
نتایج آزمون استحکام ضربه
آزمون استحکام ضربه
اندازه گیری آزمون استحکام ضربه نیز می تواند رفتار بلورینگی در روشهای مختلف سرد کردن را تصدیق کند. سرعت سرد کردن آهستهتر، بلورینگی بالاتر، گویچههای بزرگتر و کاهش انعطاف پذیری و چقرمگی را نتیجه میدهد. در اثر سرد کردن سریع، گویچههای کوچکتر با میزان بلورینگی پایینتر ایجاد میشود. گویچهها و نواحی بلوری کوچکتر، افزایش مولکولهای چسبنده درون بلور را نتیجه میدهد که باعث بهبود خواص چقرمگی مواد میشود . همچنین کارایی بیشتر بلور در بلورهای ضخیمتر و همچنین مشارکت در ایجاد ریزحفرههای نواحی اَریخت، چقرمگی شکست را بالا میبرد.
همانطور که نتایج DSC در بخش بعد نشان می دهد، هرچه سرعت سرد کردن سریع تر باشد، بلورهای ضخیم تر تشکیل می شود که دارای آنتالپی ذوب بالاتر است. این بلورهای ضخیم افزایش چقرمگی و ضربه پذیری را نتیجه می دهد که در نتایج حاصل از آزمون ضربه کاملاً مشخص است. در نتایج این آزمون، اثر تخریب سطحی مشاهده شده در نتایج آزمون کشش نیز مجدداً مشاهده می شود و نمونه سرد شده با هوا دارای کمترین استحکام ضربه است. البته تغییر در ساختار بلور، تأثیر قابل ملاحظه ای در میزان کشیدگی در نقطه پارگی دارد، در حالیکه این تأثیر در میزان ضربه پذیری بسیار کمتر است.
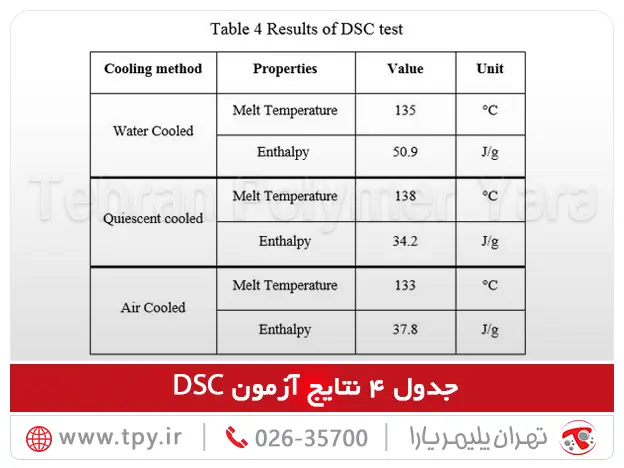
نتایج آزمون DSC
آزمون DSC
در ارتباط با نتایج آزمون DSC نیز که در نمودار ۲ و جدول ۴ آمده است، اختلاف قابل ملاحظه ای در آنتالپی ذوب سه نمونه مشاهده می شود. این اختلاف متأثر از ضخامت بلور ها در ساختار بلوری پلی اتیلن است. هرچه سرعت سرد کردن پلی اتیلن بیشتر باشد، ضخامت بلورها بیشتر است. این روند در جدول ۴ به وضوح قابل مشاهده است.
- آزمون دمای نرمشدگی
در اندازه گیری نقطه نرم شدگی به روش وایکات نیز اختلاف در دمای نرم شدگی سه نمونه کاملاً منطبق با اختلاف در آنتالپی ذوب سه نمونه و وجود بلور های ضخیم تر و در نتیجه سختی بالاتر نمونه سرد شده با آب نسبت به نمونه سرد شده با هوا و با هوای ساکن است.
آزمون تعیین چگالی
با افزایش ضخامت بلور، چگالی افزایش می یابد . برای تأیید نتایج DSC و نتایج دمای نرمشدگی Vicat، از آزمون چگالی استفاده شد. (جدول ۶) نتایج نشان می دهد هرچه سرعت سرد کردن افزایش یابد، ضخامت بلورها افزایش یافته که این افزایش ضخامت بلور، منجر به افزایش چگالی می شود.
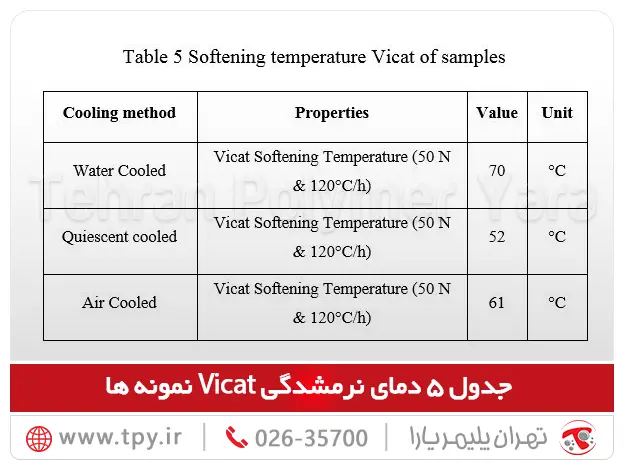
سرد کردن مخازن پلی اتیلن
ما در مقالهای جداگانه با عنوان ۱۰۰ سوال درباره مخازن و وانهای پلی اتیلن به متداولترین سوالات مربوط به تولید ، جنس محصولات ، مواد بکار رفته ، نصب مخازن و اتصالات و بسیاری موارد دیگر پاسخ دادیم. در صورتی که نیاز دارید اطلاعات بیشتری در مورد این محصولات بدست بیاورید ، پیشنهاد میکنیم تا این مقاله را مطالعه نمائید.
منابع استفاده شده برای تهیه این مقاله
R.J. Crawfoard and M.P. Kearns, Introduction to the Rotational Molding Process, in Practical Guide to Rotary Molding, Rapra Technology Limited, UK, 1-26, 2003.
F. Torres and C. Aragon, Final Product testing of Rotational Molded Natural Fiber-Reinforced Polyethylene, Polymer Testing, 25(4), 568-577, 2006.
Paul Nugent, Applied Plastics Engineering Handbook, Part 18: Rotational Molding, William Andrew, Elsevier, 311-332, 2011.
Dominick V. Rosato, Matthew V. Rosato, Donald V. Rosato, Plastic Product Material and Process Selection Handbook, Elsevier, 428-438, 2004.
K. O. Ogila, M. Shao, W. Yang, J. Tan, Rotational molding: A review of the models and materials, Express Polymer Letters, 11(10), 778–۷۹۸, ۲۰۱۷.
M. Oliveira and M. Cramez, Rotational Molding of Polyolefins: Processing, Morphology, and Properties J. Macromol. Sci. B, 40, 457-471, 2001.
M. Oliveira, M. Cramez, and R.J. Crawfoard, Structure-Properties Relationships in Rotationally Molded Polyethylene, J. Mater. Sci., 31, 2227-2240, 1996.
L. T. Pick, E. H. Jones, M. J. Oliveira, M. C. Cramez, The Effect of Cooling Rate on the Impact Performance and Dynamic Mechanical Properties of Rotationally Molded Metallocene Catalyzed Linear Low Density Polyethylene, Journal of Applied Polymer Science, 101, 1963–۱۹۷۱, ۲۰۰۶.
J. S. Godinho, Property Variations in Polyethylene Articles Produced by a Variety of Molding Methods, Doctoral Thesis, Queen’s University of Belfast, 1997.
A. Salazar, P. Frontini, and J. Rodrguez, Determination of Fracture Toughness of Propylene Polymers at Different Operating Temperatures, Engineering Fracture Mechanics, 126, 87-107, 2014.
A. Saifullah, B. Thomas, R. Cripps, K. Tabeshfar, L. Wang, C. Muryn, Fracture Toughness of Rotationally Molded Polyethylene and Polypropylene, Polymer Engineering and Science, 58 (1), 63-73, 2018.
Standard Requirements and Test Methods for Static Thermoplastic Tanks for the Above Ground Storage of Water and Chemicals Blow Molded or Rotationally Molded Polyethylene Tanks, ISIRI 16873, 2013.
D. Hansen, G. A. Bernier, Thermal Conductivity of Polyethylene: The Effects of Crystal Size, Density and Orientation on the Thermal Conductivity, Polymer Engineering and Science, 12 (3), 204-208, 1972.